Axialflussmotor mit Leiterplattenwicklung als elektromagnetische Spule
[Anleitung]Am Anfang wollte ich nur eine sehr kleine Drohne bauen. Aber schnell merkte man, dass es bei der Konstruktion einen limitierenden Faktor gibt, nämlich die Größe und das Gewicht des Motors. Selbst ein kleiner Motor ist immer noch ein diskretes Gerät und muss mit allen anderen elektronischen Komponenten und Strukturkomponenten verbunden werden. Also begann ich mich zu fragen, ob es eine Möglichkeit gibt, diese Komponenten zu kombinieren und die Qualität zu reduzieren.
IEEE SPECTRUM berichtete kürzlich über die Laune eines Ingenieurs.
Axialflussmotor mit Leiterplattenwicklung als elektromagnetische Spule
Jede Schicht des Motors gedruckt Schaltung Die Platine verfügt über einen Satz Spulen, die gestapelt und miteinander verbunden sind, um eine kontinuierliche Leiterbahn zu bilden.
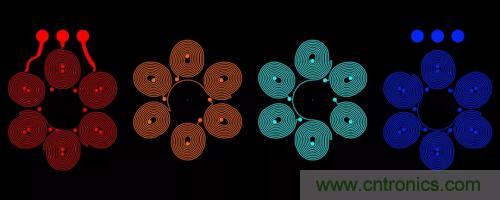
Am Anfang wollte ich nur eine sehr kleine Drohne bauen. Aber schnell merkte man, dass es bei der Konstruktion einen limitierenden Faktor gibt, nämlich die Größe und das Gewicht des Motors. Selbst ein kleiner Motor ist immer noch ein diskretes Gerät und muss mit allen anderen elektronischen Komponenten und Strukturkomponenten verbunden werden. Also begann ich mich zu fragen, ob es eine Möglichkeit gibt, diese Komponenten zu kombinieren und die Qualität zu reduzieren.
Meine Inspiration kam von der Art und Weise, wie einige Funksysteme Antennen verwenden, die aus Kupferleiterbahnen auf einem gedruckten Element bestehen Schaltung Platine (PCB). Kann mit etwas Ähnlichem ein Magnetfeld erzeugt werden, das stark genug ist, um einen Motor anzutreiben? Ich beschloss zu prüfen, ob es möglich ist, aus PCB-Leiterbahnen hergestellte elektromagnetische Spulen für die Herstellung eines Axialflussmotors zu verwenden. Bei einem Axialflussmotor sind die elektromagnetischen Spulen, die den Stator des Motors bilden, parallel zum scheibenförmigen Rotor installiert. Die Permanentmagnete sind in die Scheibe des Rotors eingebettet. Die Statorspule wird durch Wechselstrom angetrieben, um den Rotor zu drehen.
Die erste Herausforderung besteht darin, sicherzustellen, dass ich genügend magnetischen Fluss erzeugen kann, um den Rotor zu drehen. Es ist sehr einfach, eine flache Spiralspulenbahn zu entwerfen und Strom durch sie fließen zu lassen, aber ich habe den Durchmesser meines Motors auf 16 mm begrenzt, damit der Durchmesser des gesamten Motors mit dem des kleinsten fertigen bürstenlosen Motors vergleichbar ist. 16 mm bedeutet, dass ich insgesamt nur 6 Spulen unter der Rotorscheibe verbauen kann, mit etwa 10 Windungen auf jeder Spirale. Zehn Windungen reichen nicht aus, um ein ausreichend großes Magnetfeld zu erzeugen, aber heutzutage ist es einfach, mehrschichtige Leiterplatten herzustellen. Durch das Drucken in gestapelten Spulen (mit Spulen auf jeder der vier Schichten) kann ich 40 Windungen für jede Spule erhalten, genug, um einen Rotor anzutreiben.
Als das Design voranschritt, tauchte ein größeres Problem auf. Um den Motor in Rotation zu halten, ist es erforderlich, das sich dynamisch ändernde Magnetfeld zwischen Rotor und Stator zu synchronisieren. Bei einem typischen wechselstrombetriebenen Elektromotor erfolgt diese Synchronisation natürlich aufgrund der Anordnung der Bürsten, die Stator und Rotor überbrücken. Was bei einem bürstenlosen Motor benötigt wird, ist eine Steuerschaltung, die ein Rückkopplungssystem implementiert.
Links: Die fertige vierlagige Leiterplatte. Mittleres Bild: An diese Spulen werden Impulse angelegt, um einen 3D-gedruckten Rotor mit eingebetteten Permanentmagneten anzutreiben.
Rechts: Obwohl nicht so leistungsstark wie ein herkömmlicher bürstenloser Motor, ist die Platine billiger und leichter.
In einem bürstenlosen Motorantrieb, den ich zuvor gemacht habe, habe ich die Gegen-EMK als Feedback gemessen, um die Geschwindigkeit zu steuern. Der Grund für die Gegen-EMK ist, dass der rotierende Motor wie ein kleiner Generator ist, der a . erzeugt Spannung gegenüber der Spannung Wird zum Antrieb des Motors in der Statorspule verwendet. Die Induktion der elektromotorischen Gegenkraft kann Rückkopplungsinformationen über die Art und Weise liefern, wie sich der Rotor dreht, und es dem Steuerkreis ermöglichen, die Spulen zu synchronisieren. Aber in meinem PCB-Motor ist die Gegen-EMF zu schwach, um sie zu verwenden. Zu diesem Zweck habe ich einen Hall-Effekt installiert Sensor, die direkt die Änderung des Magnetfelds messen kann, um die Drehzahl des Rotors und seiner über dem Sensor rotierenden Permanentmagnete zu messen. Diese Informationen werden dann in die Motorsteuerschaltung eingegeben.
Um den Rotor selbst herzustellen, wandte ich mich dem 3D-Druck zu. Zuerst machte ich einen Rotor, den ich auf einer separaten Metallwelle montierte, aber dann begann ich, die Schnappwelle als integralen Bestandteil des Rotors zu drucken. Dies vereinfacht die physischen Komponenten auf nur den Rotor, vier Permanentmagnete, ein Lager und eine Leiterplatte, die Spulen und strukturelle Unterstützung bietet.
Ich habe schnell meinen ersten Elektromotor bekommen. Tests haben gezeigt, dass es ein statisches Drehmoment von 0.9 g cm erzeugen kann. Dies reichte nicht aus, um mein ursprüngliches Ziel zu erreichen, einen in eine Drohne integrierten Motor herzustellen, aber mir wurde klar, dass dieser Motor immer noch verwendet werden kann, um ein kleines und billiges Roboterrad mit Rädern über den Boden zu bewegen, also bestand ich darauf, zu recherchieren (Motor Normalerweise eines der teuersten Teile am Roboter). Dieser gedruckte Motor kann mit einer Spannung von 3.5 bis 7 Volt betrieben werden, obwohl er sich bei höheren Spannungen erheblich erwärmt. Bei 5 V beträgt seine Betriebstemperatur 70°C, was noch kontrollierbar ist. Es zieht ungefähr 250 mA Strom.
Derzeit arbeite ich hart daran, das Drehmoment des Motors zu erhöhen (Sie können den Forschungsfortschritt verfolgen, den ich weiterhin auf Hackaday veröffentliche: https://hackaday.io/project/39494-pcb-motor). Durch das Anbringen einer Ferritplatte auf der Rückseite der Statorspule, um die magnetischen Feldlinien der Spule einzudämmen, kann ich das Drehmoment fast verdoppeln. Ich arbeite auch daran, weitere Prototypen mit anderen Wicklungskonfigurationen und mehr Statorspulen zu entwerfen. Darüber hinaus habe ich versucht, dasselbe zu verwenden Technologie um eine elektrische Schubstange auf Leiterplatten zu bauen, die einen 3D-gedruckten Schieber antreiben kann, um auf einer Reihe von 12 Spulen zu gleiten. Außerdem teste ich einen flexiblen PCB-Prototyp, der dieselbe gedruckte Spule für den elektromagnetischen Antrieb verwendet. Mein Ziel ist es – auch wenn ich immer noch keine kleine Drohne bauen kann, die in den Himmel fliegen kann –, Roboter mit kleineren und einfacheren mechanischen Strukturen als bestehende Roboter zu bauen.
Dieser Artikel wurde in der September-Ausgabe 2018 von IEEE SPECTRUM mit dem Titel „The Printable Motor“ veröffentlicht.
Die Links:
tps65266rhbr