Motor de fluxo axial usando enrolamento de PCB como bobina eletromagnética
[Guia] No início, eu só queria fazer um drone bem pequeno. Mas logo percebi que no projeto, há um fator limitante, que é o tamanho e o peso do motor. Mesmo um motor pequeno ainda é um dispositivo discreto e precisa ser conectado a todos os outros componentes eletrônicos e estruturais. Então comecei a me perguntar se existe uma maneira de combinar esses componentes e reduzir um pouco a qualidade.
ESPECTRO IEEE relatou recentemente sobre o capricho de um engenheiro.
Motor de fluxo axial usando enrolamento de PCB como bobina eletromagnética
Cada camada do motor impressa o circuito A placa possui um conjunto de bobinas, que são empilhadas e conectadas entre si para formar um traço contínuo.
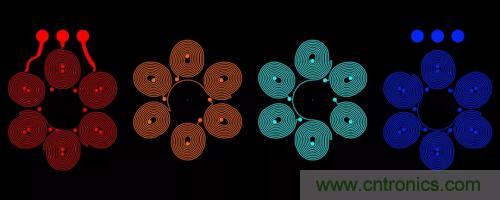
No começo, eu só queria fazer um drone bem pequeno. Mas logo percebi que no projeto, há um fator limitante, que é o tamanho e o peso do motor. Mesmo um motor pequeno ainda é um dispositivo discreto e precisa ser conectado a todos os outros componentes eletrônicos e estruturais. Então comecei a me perguntar se existe uma maneira de combinar esses componentes e reduzir um pouco a qualidade.
Minha inspiração veio de como alguns sistemas de rádio usam antenas feitas de traços de cobre em um impresso o circuito placa (PCB). Algo semelhante pode ser usado para criar um campo magnético forte o suficiente para acionar um motor? Resolvi ver se é possível usar bobinas eletromagnéticas feitas de traços de PCB para fazer um motor de fluxo axial. Em um motor de fluxo axial, as bobinas eletromagnéticas que formam o estator do motor são instaladas paralelamente ao rotor em forma de disco. Os ímãs permanentes estão embutidos no disco do rotor. A bobina do estator é acionada por corrente alternada para girar o rotor.
O primeiro desafio é garantir que posso criar fluxo magnético suficiente para girar o rotor. Projetar um traço de bobina espiral plana e deixar a corrente fluir através dele é muito simples, mas eu limitei o diâmetro do meu motor a 16 mm para que o diâmetro de todo o motor seja comparável ao do menor motor sem escova acabado. 16 mm significa que só posso instalar um total de 6 bobinas sob o disco do rotor, com cerca de 10 voltas em cada espiral. Dez voltas não são suficientes para gerar um campo magnético grande o suficiente, mas hoje em dia é fácil fazer PCBs multicamadas. Imprimindo em bobinas empilhadas (com bobinas em cada uma das quatro camadas), posso obter 40 voltas para cada bobina, o suficiente para girar um rotor.
À medida que o design avançava, um problema maior surgiu. Para manter o motor girando, é necessário sincronizar o campo magnético que muda dinamicamente entre o rotor e o estator. Em um motor elétrico típico movido por corrente alternada, essa sincronização ocorre naturalmente devido ao arranjo das escovas que ligam o estator e o rotor. Em um motor sem escovas, o que é necessário é um circuito de controle que implemente um sistema de feedback.
Esquerda: A placa de circuito impresso de quatro camadas concluída. Imagem do meio: pulsos são aplicados a essas bobinas para acionar um rotor impresso em 3D com ímãs permanentes incorporados.
À direita: embora não seja tão potente quanto um motor sem escova tradicional, o PCB é mais barato e mais leve.
Em um motor brushless que fiz antes, medi o EMF traseiro como feedback para controlar a velocidade. A razão para o back-EMF é que o motor giratório é como um pequeno gerador, gerando um Voltagem oposto ao Voltagem usado para acionar o motor na bobina do estator. A indução da força eletromotriz de retorno pode fornecer informações de feedback sobre a maneira como o rotor gira e permite que o circuito de controle sincronize as bobinas. Mas no meu motor PCB, o EMF traseiro é muito fraco para usar. Para isso, instalei um efeito Hall sensor, que pode medir diretamente a mudança no campo magnético para medir a velocidade do rotor e seus ímãs permanentes girando acima do sensor. Esta informação é então inserida no circuito de controle do motor.
Para fazer o próprio rotor, recorri à impressão 3D. No início, fiz um rotor, que instalei em um eixo de metal separado, mas depois comecei a imprimir o eixo de encaixe como parte integrante do rotor. Isso simplifica os componentes físicos para apenas o rotor, quatro ímãs permanentes, um rolamento e um PCB que fornece bobinas e suporte estrutural.
Rapidamente ganhei meu primeiro motor elétrico. Os testes mostraram que pode gerar um torque estático de 0.9 g cm. Isso não foi suficiente para cumprir meu objetivo original de fabricar um motor integrado a um drone, mas percebi que esse motor ainda poderia ser usado para impulsionar uma roda de robô pequena e barata ao longo do solo com rodas, então insisti em pesquisar (motor Normalmente uma das peças mais caras do robô). Este motor impresso pode operar com uma tensão de 3.5 a 7 volts, embora vá aquecer significativamente em tensões mais altas. A 5 V, sua temperatura de operação é de 70 ° C, ainda controlável. Ele consome aproximadamente 250 mA de corrente.
Atualmente, tenho trabalhado muito para aumentar o torque do motor (você pode acompanhar o andamento da pesquisa que continuo publicando no Hackaday https://hackaday.io/project/39494-pcb-motor). Ao adicionar uma folha de ferrite na parte traseira da bobina do estator para conter as linhas do campo magnético da bobina, posso quase dobrar o torque. Também estou trabalhando no projeto de outros protótipos com diferentes configurações de enrolamento e mais bobinas de estator. Além disso, tenho tentado usar o mesmo tecnologia para construir uma haste elétrica de PCB que pode acionar um controle deslizante impresso em 3D para deslizar em uma fileira de 12 bobinas. Além disso, estou testando um protótipo de PCB flexível que usa a mesma bobina impressa para realizar acionamento eletromagnético. Meu objetivo é - mesmo que eu ainda não consiga fazer um pequeno drone que possa voar até o céu - começar a fabricar robôs com estruturas mecânicas menores e mais simples do que os robôs existentes.
Este artigo foi publicado na edição de setembro de 2018 do IEEE SPECTRUM, intitulado “The Printable Motor”.
Os links:
tps65266rhbr