Motor de flujo axial que utiliza bobinado de PCB como bobina electromagnética
[Guía] Al principio, solo quería hacer un dron muy pequeño. Pero pronto se dio cuenta de que en el diseño hay un factor limitante, que es el tamaño y el peso del motor. Incluso un motor pequeño sigue siendo un dispositivo discreto y debe conectarse a todos los demás componentes electrónicos y componentes estructurales. Entonces comencé a preguntarme si hay una manera de combinar estos componentes y reducir algo de calidad.
IEEE SPECTRUM informó recientemente sobre el capricho de un ingeniero.
Motor de flujo axial que utiliza bobinado de PCB como bobina electromagnética
Cada capa del motor impresa circuito El tablero tiene un conjunto de bobinas, que se apilan y conectan entre sí para formar una traza continua.
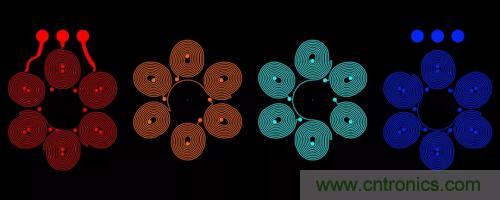
Al principio, solo quería hacer un dron muy pequeño. Pero pronto se dio cuenta de que en el diseño hay un factor limitante, que es el tamaño y el peso del motor. Incluso un motor pequeño sigue siendo un dispositivo discreto y debe conectarse a todos los demás componentes electrónicos y componentes estructurales. Entonces comencé a preguntarme si hay una manera de combinar estos componentes y reducir algo de calidad.
Mi inspiración provino de cómo algunos sistemas de radio usan antenas hechas de trazas de cobre en un impreso circuito placa (PCB). ¿Se puede usar algo similar para crear un campo magnético lo suficientemente fuerte como para impulsar un motor? Decidí ver si es posible usar bobinas electromagnéticas hechas de trazas de PCB para hacer un motor de flujo axial. En un motor de flujo axial, las bobinas electromagnéticas que forman el estator del motor se instalan paralelas al rotor en forma de disco. Los imanes permanentes están incrustados en el disco del rotor. La bobina del estator es accionada por corriente alterna para hacer girar el rotor.
El primer desafío es asegurarme de que puedo crear suficiente flujo magnético para hacer girar el rotor. Diseñar un trazo de bobina en espiral plana y dejar que la corriente fluya a través de él es muy simple, pero limité el diámetro de mi motor a 16 mm para que el diámetro de todo el motor sea comparable al del motor sin escobillas con acabado más pequeño. 16 mm significa que solo puedo instalar un total de 6 bobinas debajo del disco del rotor, con aproximadamente 10 vueltas en cada espiral. Diez vueltas no son suficientes para generar un campo magnético lo suficientemente grande, pero hoy en día es fácil hacer PCB multicapa. Al imprimir en bobinas apiladas (con bobinas en cada una de las cuatro capas), puedo obtener 40 vueltas para cada bobina, lo suficiente para hacer girar un rotor.
A medida que avanzaba el diseño, surgió un problema mayor. Para mantener el motor girando, es necesario sincronizar el campo magnético que cambia dinámicamente entre el rotor y el estator. En un motor eléctrico típico impulsado por corriente alterna, esta sincronización ocurre naturalmente debido a la disposición de las escobillas que unen el estator y el rotor. En un motor sin escobillas, lo que se necesita es un circuito de control que implemente un sistema de retroalimentación.
Izquierda: La placa de circuito impreso de cuatro capas completa. Imagen central: se aplican pulsos a estas bobinas para impulsar un rotor impreso en 3D con imanes permanentes integrados.
Derecha: aunque no es tan potente como un motor sin escobillas tradicional, la PCB es más barata y ligera.
En un motor sin escobillas que hice antes, medí el EMF trasero como retroalimentación para controlar la velocidad. La razón del back-EMF es que el motor giratorio es como un pequeño generador, generando un voltaje opuesto a la voltaje utilizado para impulsar el motor en la bobina del estator. La inducción de la fuerza contraelectromotriz puede proporcionar información de retroalimentación sobre la forma en que gira el rotor y permitir que el circuito de control sincronice las bobinas. Pero en mi motor de PCB, el EMF posterior es demasiado débil para usarlo. Para ello instalé un efecto Hall sensor, que puede medir directamente el cambio en el campo magnético para medir la velocidad del rotor y sus imanes permanentes que giran sobre el sensor. Luego, esta información se ingresa en el circuito de control del motor.
Para hacer el rotor en sí, recurrí a la impresión 3D. Al principio, hice un rotor, que instalé en un eje de metal separado, pero luego comencé a imprimir el eje a presión como parte integral del rotor. Esto simplifica los componentes físicos a solo el rotor, cuatro imanes permanentes, un cojinete y una PCB que proporciona bobinas y soporte estructural.
Rápidamente obtuve mi primer motor eléctrico. Las pruebas han demostrado que puede generar un par estático de 0.9 g cm. Esto no fue suficiente para cumplir con mi objetivo original de fabricar un motor integrado en un dron, pero me di cuenta de que este motor aún podía usarse para impulsar una rueda de robot pequeña y barata por el suelo con ruedas, así que insistí en investigar (motor Normalmente una de las piezas más caras del robot). Este motor impreso puede funcionar a un voltaje de 3.5 a 7 voltios, aunque se calentará significativamente a voltajes más altos. A 5 V, su temperatura de funcionamiento es de 70 ° C, que aún es controlable. Consume aproximadamente 250 mA de corriente.
Actualmente, he estado trabajando duro para aumentar el par del motor (puede seguir el progreso de la investigación que sigo publicando en La-Tecnologia https://la-tecnologia.io/project/39494-pcb-motor). Al agregar una lámina de ferrita a la parte posterior de la bobina del estator para contener las líneas del campo magnético de la bobina, casi puedo duplicar el torque. También estoy trabajando en el diseño de otros prototipos con diferentes configuraciones de devanados y más bobinas de estator. Además, he estado intentando usar el mismo la tecnología para construir una varilla de empuje eléctrica de PCB que pueda impulsar un control deslizante impreso en 3D para que se deslice sobre una fila de 12 bobinas. Además, estoy probando un prototipo de PCB flexible que utiliza la misma bobina impresa para realizar un accionamiento electromagnético. Mi objetivo es, incluso si todavía no puedo fabricar un pequeño dron que pueda volar hacia el cielo, comenzar a fabricar robots con estructuras mecánicas más pequeñas y simples que los robots existentes.
Este artículo se publicó en la edición de septiembre de 2018 de IEEE SPECTRUM, titulado "El motor imprimible".
Los enlaces:
tps65266rhbr