Moteur à flux axial utilisant un bobinage PCB comme bobine électromagnétique
[Guide]Au départ, je voulais juste faire un tout petit drone. Mais s'est vite rendu compte que dans la conception, il y a un facteur limitant, c'est la taille et le poids du moteur. Même un petit moteur est toujours un appareil discret et doit être connecté à tous les autres composants électroniques et composants structurels. J'ai donc commencé à me demander s'il y avait un moyen de combiner ces composants et de réduire une certaine qualité.
IEEE SPECTRUM a récemment rendu compte de la fantaisie d'un ingénieur.
Moteur à flux axial utilisant un bobinage PCB comme bobine électromagnétique
Chaque couche du moteur imprimée circuit carte a un ensemble de bobines, qui sont empilées et connectées les unes aux autres pour former une trace continue.
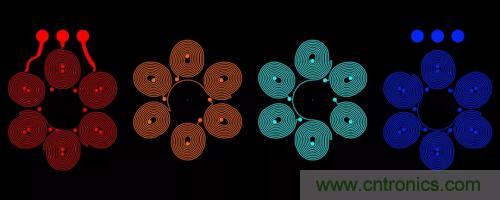
Au début, je voulais juste faire un tout petit drone. Mais s'est vite rendu compte que dans la conception, il y a un facteur limitant, c'est la taille et le poids du moteur. Même un petit moteur est toujours un appareil discret et doit être connecté à tous les autres composants électroniques et composants structurels. J'ai donc commencé à me demander s'il y avait un moyen de combiner ces composants et de réduire une certaine qualité.
Mon inspiration est venue de la façon dont certains systèmes radio utilisent des antennes faites de traces de cuivre sur un imprimé circuit carte (PCB). Quelque chose de similaire peut-il être utilisé pour créer un champ magnétique suffisamment puissant pour entraîner un moteur ? J'ai décidé de voir s'il était possible d'utiliser des bobines électromagnétiques constituées de traces de PCB pour fabriquer un moteur à flux axial. Dans un moteur à flux axial, les bobines électromagnétiques formant le stator du moteur sont installées parallèlement au rotor en forme de disque. Les aimants permanents sont intégrés dans le disque du rotor. La bobine du stator est entraînée par un courant alternatif pour faire tourner le rotor.
Le premier défi est de m'assurer que je peux créer suffisamment de flux magnétique pour faire tourner le rotor. Concevoir une trace de bobine en spirale plate et laisser passer le courant à travers elle est très simple, mais j'ai limité le diamètre de mon moteur à 16 mm afin que le diamètre de l'ensemble du moteur soit comparable à celui du plus petit moteur brushless fini. 16 mm signifie que je ne peux installer qu'un total de 6 bobines sous le disque du rotor, avec environ 10 tours sur chaque spirale. Dix tours ne suffisent pas pour générer un champ magnétique suffisamment grand, mais de nos jours, il est facile de fabriquer des PCB multicouches. En imprimant en bobines empilées (avec des bobines sur chacune des quatre couches), je peux obtenir 40 tours pour chaque bobine, assez pour faire tourner un rotor.
Au fur et à mesure que la conception avançait, un problème plus important est apparu. Afin de maintenir le moteur en rotation, il est nécessaire de synchroniser le champ magnétique changeant dynamiquement entre le rotor et le stator. Dans un moteur électrique typique entraîné par un courant alternatif, cette synchronisation se produit naturellement en raison de la disposition des balais qui relient le stator et le rotor. Dans un moteur sans balais, il faut un circuit de commande qui implémente un système de rétroaction.
À gauche : la carte de circuit imprimé à quatre couches terminée. Image du milieu : des impulsions sont appliquées à ces bobines pour entraîner un rotor imprimé en 3D avec des aimants permanents intégrés.
À droite : bien qu'il ne soit pas aussi puissant qu'un moteur sans balai traditionnel, le PCB est moins cher et plus léger.
Dans un entraînement de moteur sans balais que j'ai fait auparavant, j'ai mesuré la force contre-électromotrice comme rétroaction pour contrôler la vitesse. La raison de la force contre-électromotrice est que le moteur rotatif est comme un petit générateur, générant un Tension à l'opposé de la Tension utilisé pour entraîner le moteur dans la bobine du stator. L'induction de la force contre-électromotrice peut fournir des informations de rétroaction sur la façon dont le rotor tourne et permettre au circuit de commande de synchroniser les bobines. Mais dans mon moteur PCB, la force contre-électromotrice est trop faible pour être utilisée. Pour cela, j'ai installé un effet Hall capteur, qui permet de mesurer directement la variation du champ magnétique pour mesurer la vitesse du rotor et de ses aimants permanents tournant au dessus du capteur. Cette information est ensuite entrée dans le circuit de commande du moteur.
Pour fabriquer le rotor lui-même, je me suis tourné vers l'impression 3D. Au début, j'ai fabriqué un rotor que j'ai installé sur un arbre métallique séparé, mais j'ai ensuite commencé à imprimer l'arbre à ressort en tant que partie intégrante du rotor. Cela simplifie les composants physiques au seul rotor, quatre aimants permanents, un roulement et un PCB qui fournit des bobines et un support structurel.
J'ai rapidement eu mon premier moteur électrique. Des tests ont montré qu'il peut générer un couple statique de 0.9 g cm. Ce n'était pas suffisant pour atteindre mon objectif initial de fabriquer un moteur intégré dans un drone, mais j'ai réalisé que ce moteur pouvait toujours être utilisé pour propulser une petite roue de robot bon marché le long du sol avec des roues, j'ai donc insisté pour faire des recherches (moteur Habituellement l'une des pièces les plus chères du robot). Ce moteur imprimé peut fonctionner à une tension de 3.5 à 7 volts, bien qu'il chauffe considérablement à des tensions plus élevées. A 5 V, sa température de fonctionnement est de 70°C, ce qui reste maîtrisable. Il consomme environ 250 mA de courant.
Actuellement, je travaille dur pour augmenter le couple du moteur (vous pouvez suivre l'avancée des recherches que je continue de publier sur Hackaday https://hackaday.io/project/39494-pcb-motor). En ajoutant une feuille de ferrite à l'arrière de la bobine du stator pour contenir les lignes de champ magnétique de la bobine, je peux presque doubler le couple. Je travaille également sur la conception d'autres prototypes avec différentes configurations de bobinages et davantage de bobines de stator. De plus, j'ai essayé d'utiliser le même sans souci pour construire une tige de poussée électrique pour PCB capable de faire glisser un curseur imprimé en 3D sur une rangée de 12 bobines. De plus, je teste un prototype de PCB flexible qui utilise la même bobine imprimée pour effectuer un entraînement électromagnétique. Mon objectif est, même si je ne parviens toujours pas à fabriquer un petit drone capable de voler dans le ciel, de commencer à créer des robots dotés de structures mécaniques plus petites et plus simples que les robots existants.
Cet article a été publié dans le numéro de septembre 2018 de IEEE SPECTRUM, intitulé « The Printable Motor ».
Le lien:
tps65266rhbr